Hot Products
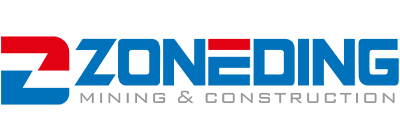
We provide a variety of mining and processing equipment, including feeders, rock crushers, grinders, classifying & screening machines, washing machines, gravity separators, flotation machines, magnetic separators, electric separators, dewatering equipmentand laboratory mineral processing equipment, etc.